
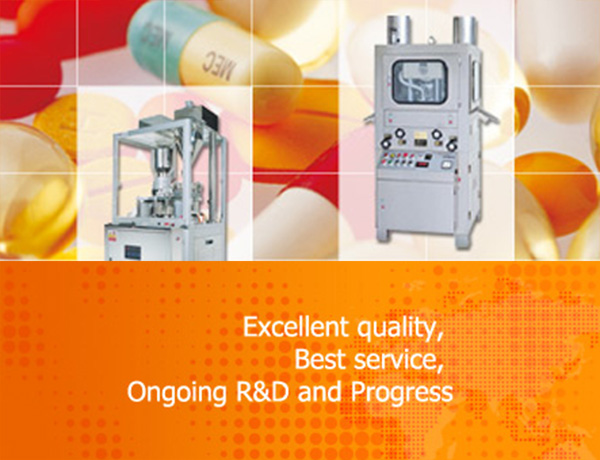
WRAP AROUND LABELING MACHINE is suitable for round-shaped products of different specifications. D.I.Y. design and simple operation means you won't require professionally trained technicians to operate this machine. With an adjustable guide rail, and a hand wheel to adjust the height of the applicator, the machine has the ability to label different sized round products. It can operate as an independent machine or as a part of a production/assembly line.
Voltage | 110/220 VAC, 50/60 HZ, 1 PHASE |
Power | 760 VA |
Controls | NETCON TOUCH SCREEN |
Converyor Speed | 20 M/MIN MAX |
Dispensing Speed | 40 M/MIN MAX |
Drive | STEPPER MOTOR |
Applicator Height | 150/220 MM |
Label Size | H:150 mm x L:300 mm MAX |
Converyor Width | 110 mm |
Spool Diameter | 46/76 mm |
Optional | HOT FOIL PRINTER |
LENGTH 2,000 MM
WIDTH 1,120 MM
HEIGHT 1,050 MM
The frame and main components of the machine are made from SUS #304 stainless steel and anodized aluminum.